Level II (Veteran Producer) is the serious level of concrete products production. Companies are striving to produce a high production output of wet cast slabs, cast stone or veneer stone and specialty concrete products. This level of concrete equipment offers a versatile concrete wet cast machine system that can make a wide variety of concrete products at a high production rate. We have named this particular concrete wet cast equipment the “HYBRID” series. The Hybrid has the combination of being able to automatically dose veneer stone, wet cast slab and cast stone products all on the same equipment production line. The other unique advantage is the system is able to demold all the different products either automatically or semi-automatic depending on the types of products you are producing. The handling of heavy molds and products are stacked and unstacked automatically. The system requires only one fork lift for taking products to and from curing room.
You literally have a wet cast machine system that is idea for making a wide variety of products without having to invest into a second production line or keep a manual line of people making veneer stone. You reduce labor, increase quality consistency of your products and grow your business, all with one machine system.
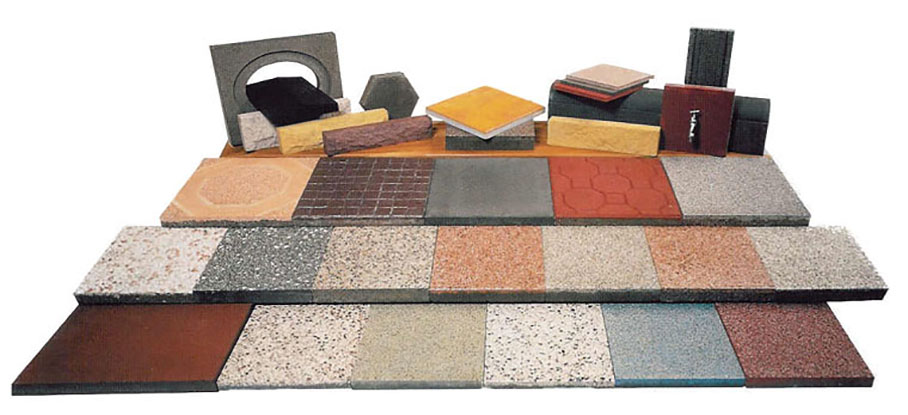
Wide variety of wet cast slabs, cast stone, veneer stone and specialty landscape units are made on Hybrid wet cast machine
Plant designs are normally fitted into existing plant setups. They can also can be planned for all new building structures designed around the manufacturing equipment for operational efficiencies. I have seen repeatedly companies and individuals entering the market for the first time choosing the level II investment package. They are doing this with their new products ideas and want to produce at high volumes with low labor cost having the flexibility to make a wide range of products.
The majority of users purchasing the Hybrid concrete wet cast equipment have been in concrete products manufacturing business for many years. Typically, buyers have either been manufacturing, buying or reselling products before purchasing this level of wet cast equipment package. If they have not previously been in the industry, it is important to the success of the company to have a strong sales and marketing team to sell the large volume and amount of wet cast products this machine line can produce.
All aspects of the concrete batching, mixing, casting and palletizing processes are generally semi-automatic. Watch Level 2 Machinery in operation.
Click image to view larger image.
A typical Hybrid production plant will include a batch plant, concrete mixer, cement silo with all the accessary equipment. This will ensure the concrete mix is being weighed, premeasured, mixed thoroughly prior to being placed into the wet cast machinery. Below are the production outputs that a typical wet cast products plant could expect for making veneer stone with semi manual demolding or wet cast slabs with automatic demolding.
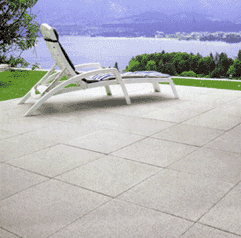
Concrete West Cast Textured Slabs
Production Up to per Hour
18″x18″x2″(45x45x4cm)
Veneer Stone 6 sq.ft. (.55 m2)
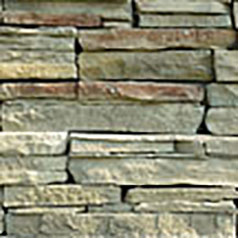
Veneer Stone Ledge Stone Series
Production Up to per Hour
720 units per hour
1500sq.ft. (139 m2 )
The production line is designed to operate on a cycle time of approximately 10-20 seconds depending on the specific products you are wanting to produce. The cycle time is dependent on semi-automatic functions undertaken during the manufacturing process.
TYPICIAL PRODUCTION LINE
The concrete slab products come in various sizes and are manufactured in either polyurethane(PU) or ABS molds positioned within the wooden or carrier for handling purposes. The carrier production area size depends on your production and product requirements. A common sized carrier is 30”x48” (762×1220 mm) which allows for a very versatile range of products to be made while still gaining and medium output production of products in a daily production shift.
The machine system consists of several individual machine components that when connected together make a complete operating manufacturing system. A wide variety of products such as concrete slabs, veneer stone, cast stone, retaining walls, lawn edger’s, steps, and landscape units are common products made on the machinery.
The first step in explaining the process and journey of making wet cast concrete products starts from the product curing room. Yesterday’s production carriers, which hold the products that were made have been cured and are brought out of the curing room. A single stack of carriers is placed into the wet cast machine system for demolding and dosing. Then the molds are vibrated, restacked and taken to the curing room for overnight storage and curing. Listed below is a general summary of the individual equipment items and descriptions that make up a wet cast system.
Single Stack Infeed Conveyor
This unit holds one cured stack of carriers that is taken from the curing room. The Single Stack Infeed Conveyor automatically conveys a complete stacker of carriers into the lowerator. The infeed conveyor is loaded by fork lift.
Lowerator Stack In. The lowerator accepts a complete stack of full or empty carriers into the unloading position. The stack is loaded onto the infeed conveyor by forklift truck, and then positioned to begin unloading of stack of carriers. When the stack is empty the Lowerator Stack In is automatically fed another stack that is into the Lowerator.
The Lowerator Stack In can hold up to 2 full stacks of carriers in readiness for entering the Lowerator.
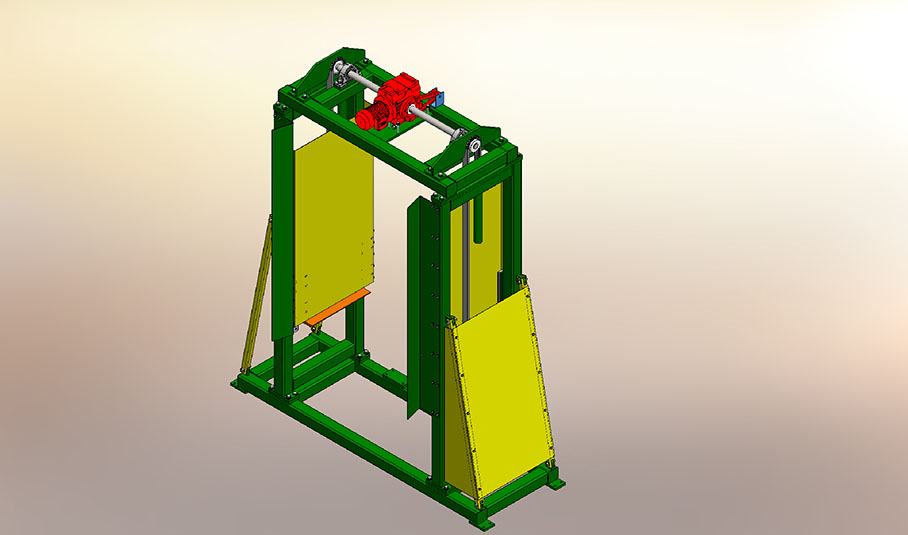
Lowerator Stack In is used for unloading stacks of carriers & dispensing one carrier down the production line.
The Lowerator separates the stack of carriers and conveys single carriers at regular intervals onto the product wet line conveyor. The lowerator lifts the unstacks the carriers by means of mechanically synchronised vertical slide carriages which raise and lower during operations.
The Lowerator lifts the entire stack but the bottom one carrier in the stack. The bottom carrier is transported out of the Lowerator onto the wet line conveyor.
The process continues until the stack is empty and another stack is inserted into the Lowerator Stack In process starts over again.
Production Carrier Wet Conveyor line
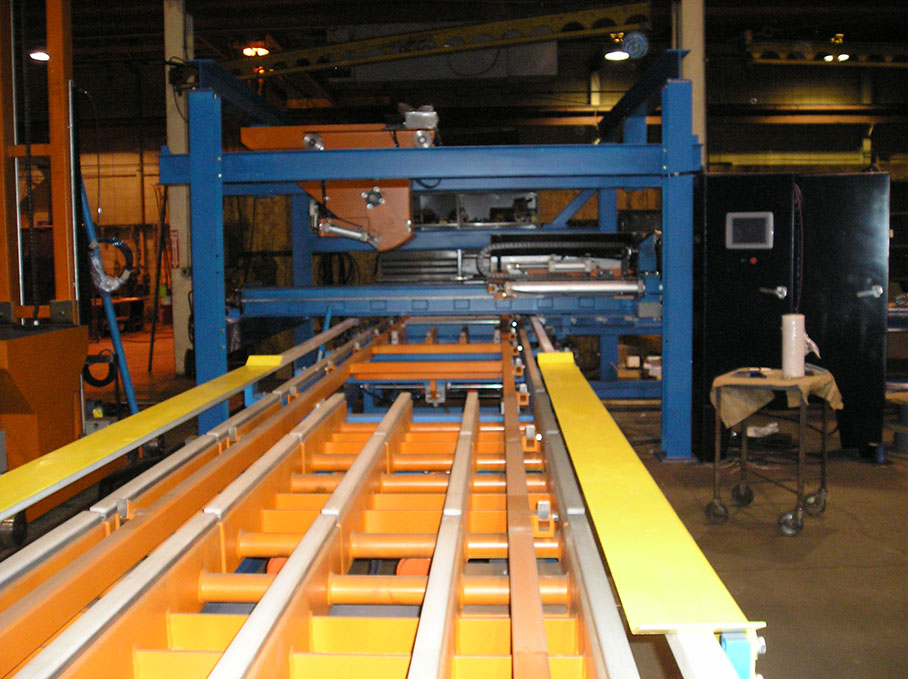
Wet Conveyor transports carriers and mold to dosing area where molds are automatically filled.
The carrier conveyor system transports and positions the carriers to the correct stations along the wet cast system. Exact position placement of the carriers is integrated with fully automatic PLC controls.
Production Carrier Turnover Station
The production carrier turnover device rotates the production carrier and product mold together 180 degrees leaving the molds and concrete product separated from the carrier upside down on a belted conveyor.
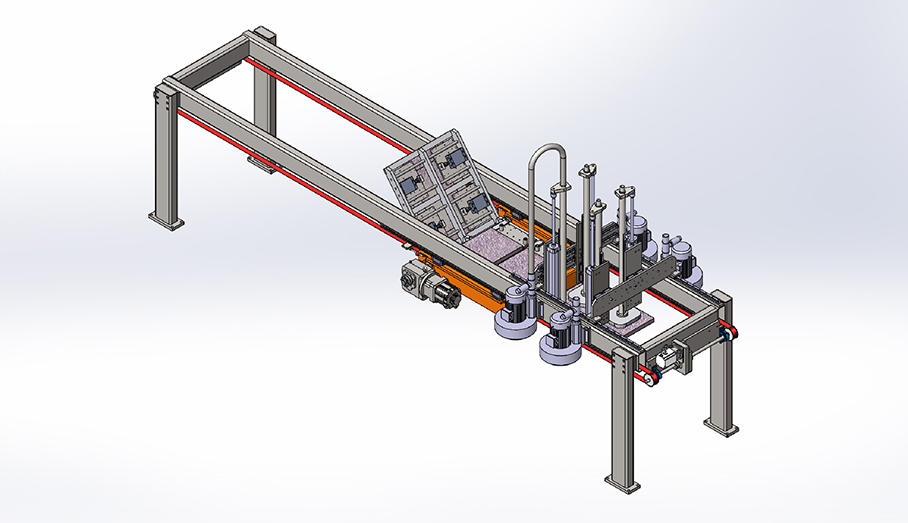
Hybrid Combination Turnover & automatic vacuum demolder for Palletizing a wide variety of Products
The carrier is rotated back into its original position in the production line. At the same time this is occurring the molds that were placed on the belted conveyor are being removed from the rubber molds. Once the concrete product is quickly de-molded, the rubber molds are then placed back into the carrier while the production line is functioning, but prior to dosing of concrete molds with concrete.
The system also has the vacuum demolding system for automatic demolding concrete wet cast slabs in the same working station. When using this option, the products are demolded out of the molds automatically and stacked vertically or placed flat onto belted conveyor line.
Spare Stations.
Spare stations can be provided which adds more versatility to the overall system. Additional stations are commonly used for the returning of the mold to the empty carrier and for the manual application of release oil if needed. Each machine system can be customized to your exacting specifications and production requirements. This will depend greatly on the dimensions of the products you are wanting to produce along with your packaging requirements. To start discussion on these topics please feel free to pick up the phone and call me at 314-960-0540.
Mold Oiler Spray Booth
The Mold Oiler automatically coats each mold with release agent, to prevent product sticking in the mold during the de-molding process.
When a carrier arrives into the mold oiler spray booth, the atomising air and oil supply are automatically turned on and the spray nozzles start automatically covering the mold with the proper amount of release oil.
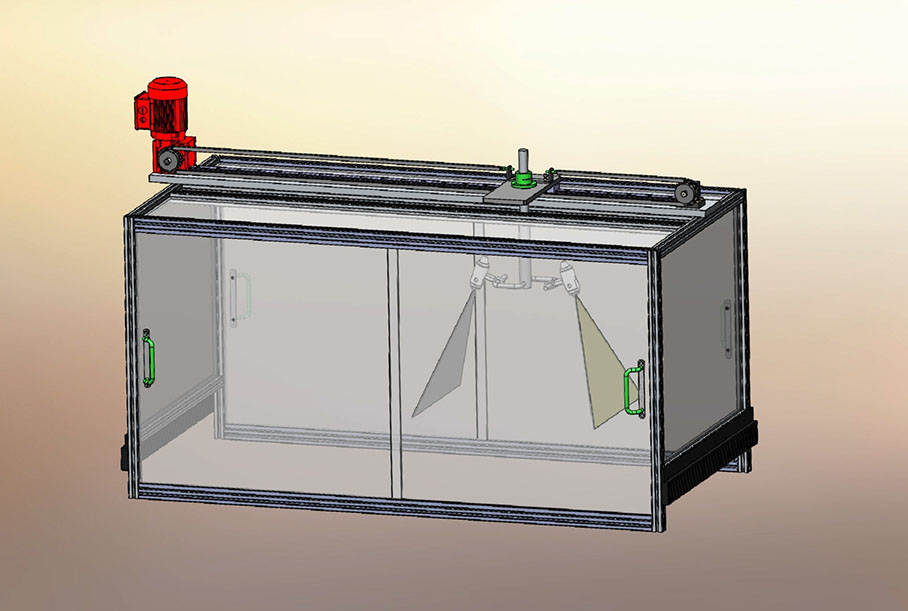
Mold Oiler Spray Booth is used to prevent product sticking in the mold during the de-molding process and adds extra mold life to molds.
An air mist filter unit creates a negative pressure inside the enclosure, drawing vapour from the enclosure and removing oil particles. By doing this any oil mist outside the unit is highly reduced.
Two or more air atomised automatic spray guns are mounted inside an enclosure with electrostatic filters. The spray guns are specifically designed for this application and spray over the entire area of the mold.
Mold Spray Guns
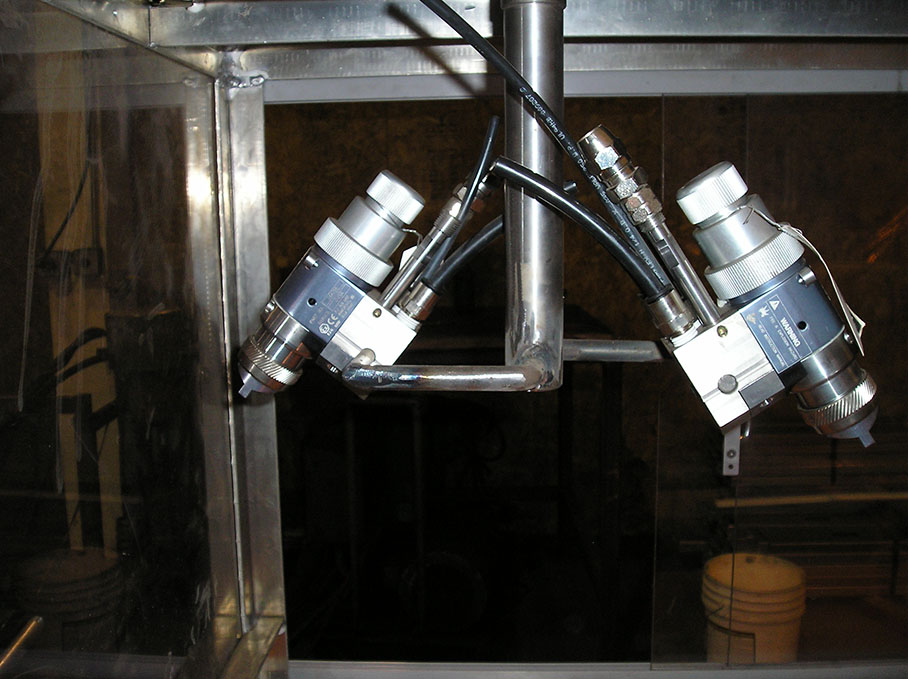
Spray Guns ensure that every part of the product mold is covered & adds longer life to molds and prevents product sticking.
The positions of the nozzles in the vertical and longitudinal directions ensure that every part of the mold is covered with oil to prevent any sticking of concrete to the mold. By using an mold oiler a producer will prevent concrete build-up on the mold surface which can affect the texture of the product being made. This will save the producer by making a better quality unit with less mold replacement cost.
Mold Doser Systems
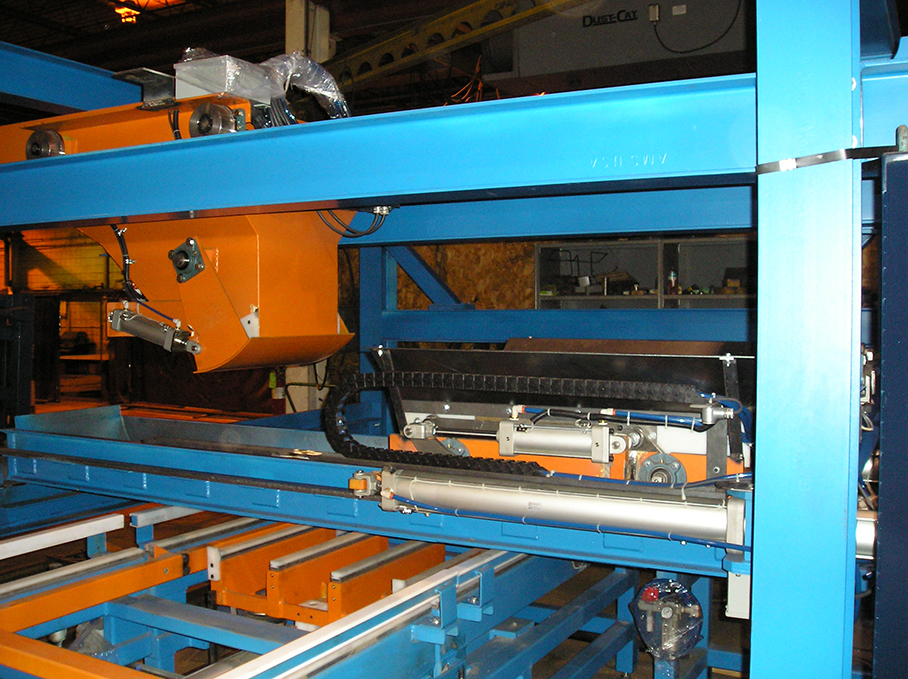
Dosing Systems can be offered in 3-color screw weigh doser system, weigh dosing, volumetric and semi manual options.
The filling of the molds with concrete mix is done with volumetric doser systems for automatic filling of the molds. A single or dual screw dosing system is optional and suitable for dosing the length of the carrier and can be designed to your requirements. We use both weigh batch and volumetric weighs systems based on concrete product specifications, output and budget requirements.
Wet Cast Concrete Vibration Table Stations
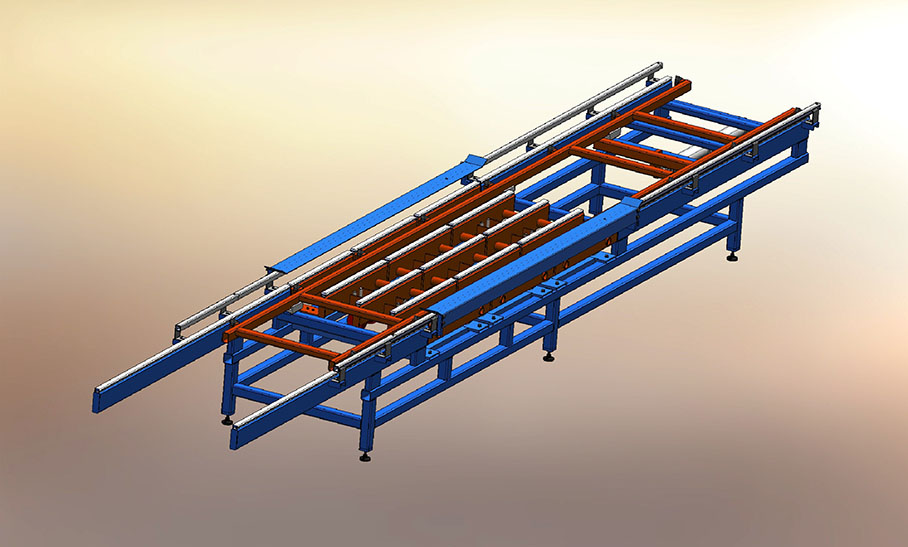
Vibration conveyor has multiple vibrating tables that vibrate allowing products to compact and achieve uniform height control.
Once the mold has been filled with concrete the production carrier supporting the mold is automatically moved onto and across the intense wet cast vibration stations. The combination of vibration stations are fitted with electric vibrators which vibrate the concrete in the molds to the desired product height and compacted strength. The vibration motors utilize adjustable weights that can change the amount of vibration amplitude force applied into the molds.
Adjustable Frequency & Amplitude Vibration Table
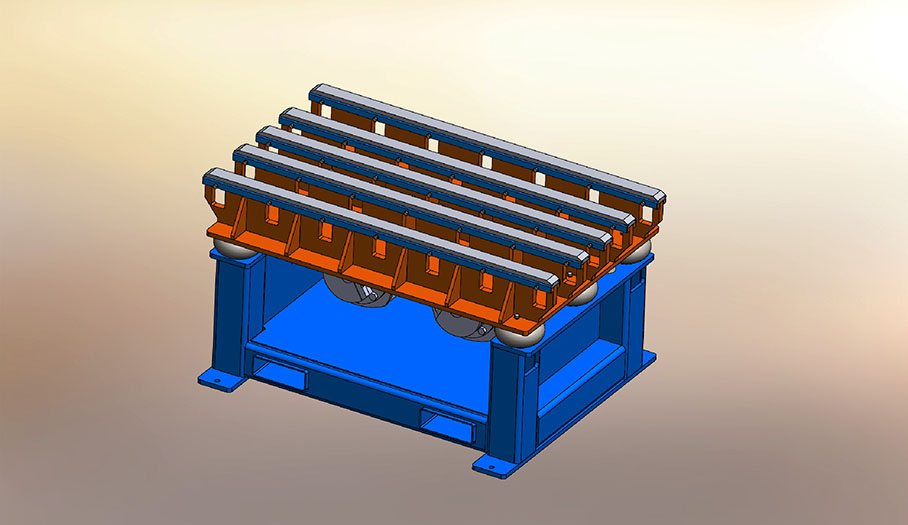
Vibration table has vibrators with frequency & amplitude controls for adjustable product compaction and textures.
A frequency controller allows the operator greater versatility during the mold filling process and vibration stages in achieving greater consistencies in product height control, compaction and desired surface textures. In addition, the controller’s capabilities can reduce overall cycle time and greatly helps producers in being able be manufacture consistent product thicknesses with a press of a button.
Elevator Stack Out
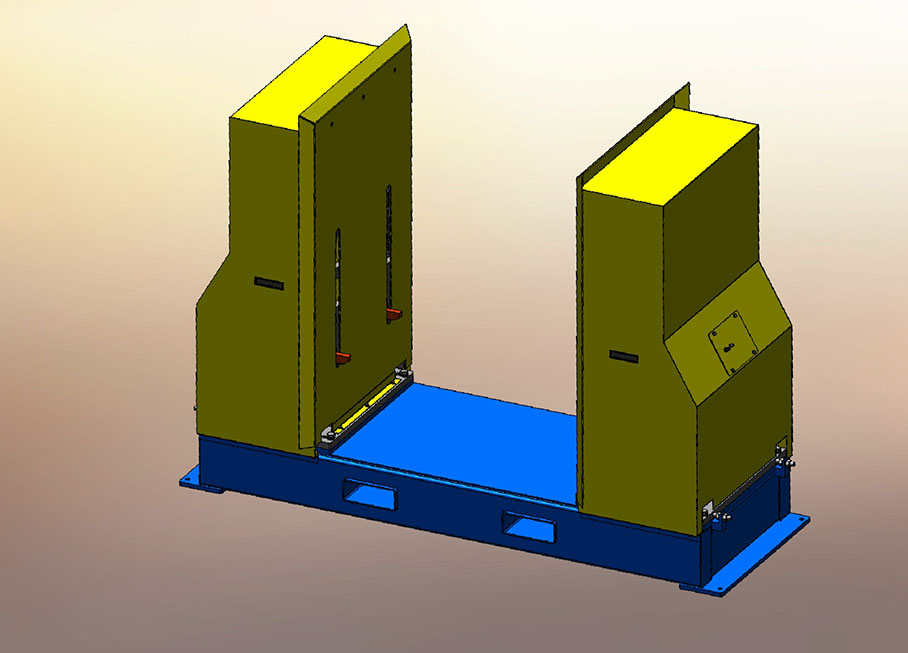
Elevator Stack Out is used for forming stacks of molds & carriers on top each.
The Elevator Stack Out individual carriers and makes them into a transport stack that is then taken to curing area. A transport stack that is normally about twenty-two layers high. The sequence starts with carriers being conveyed from the wet cast line after being individually dosed with concrete to the lowerator stack out. Once they are in position the lowerator lifts the carrier by means of mechanically synchronised vertical slide carriages. The stack is created from a bottom up motion process until a full stack is formed. The completed stack is then ready to be taken to a curing area by fork lift.
PLC control system
The PLC (Program Logic Controller) is programmed to operate the entire system and is designed to be user friendly so any person along the production line can stop the system at any time. The controls are based on the theory to make the machinery system smarter, so the human element of operating machinery is reduced. Our goal is to create a smarter wet cast slab machine control package that makes your operators job more efficient and productive. This helps producers ensure a consistent operation and make top quality wet cast slab, cast stone or veneer stone products. It brings a tool that is reliable and can fully meet the expectations of any producer.
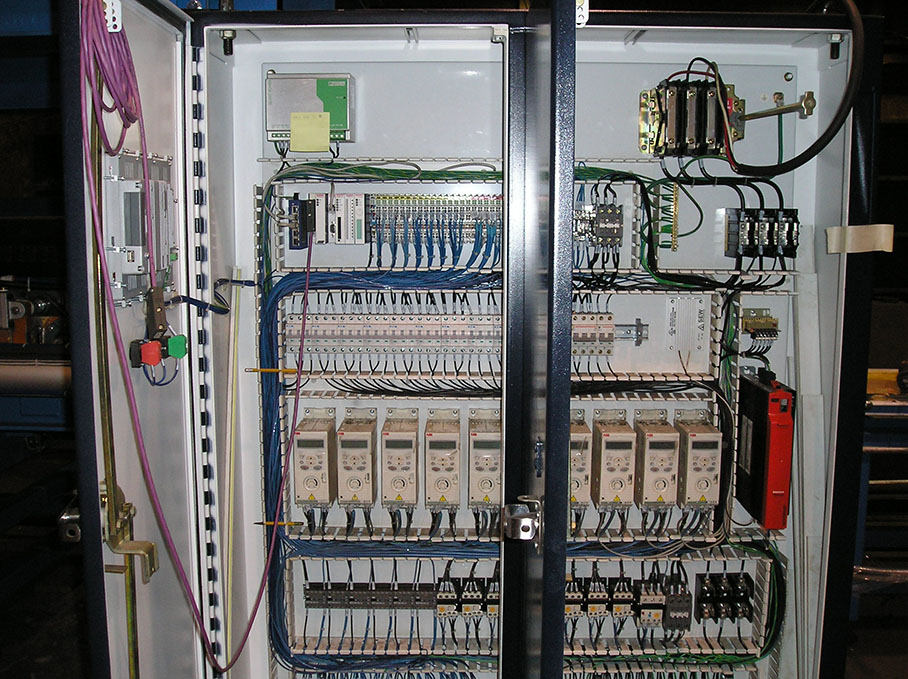
PLC hardware controls are mounted in dust proof enclosures for ease of service and trouble shooting.
If you have more questions about the system, please feel free to pick up the phone and give me a call at 314-960-0540. You can also search and get answers to many of question by downloading “The Only Block Machine Guide You’ll Ever need“.
What is unique about working with Global Machine from Anyone else?
Our machine systems have been widely installed in North America many countries. When a person is considering the purchase of a machine system from us I always try to explain to them the benefits and unique differences of working with us over anyone in the world market. I hope these reasons will help you to better understand my company and provide valuable information to help in your journey of choosing our equipment for your needs.
If you might be challenged and confused about the small world of wet cast machinery systems on the market today, there are many major differences. Some non-industry manufacturers may try to confuse you with many statements that mislead people and make them believe the we cast industry is as simple as buying a car. Have suppliers been telling you they make the best machine? Are promises being made they will guarantee the best price or delivery time in the world? The wet cast industry is simple or just buy our machine and get started today and I can ship to you, and you will have no problems? Please read the below and I think you will find the honest answers you are looking to have.
Global Machine Market is a USA company, real and reputable. My grandfather Harry Fleming family started making concrete machinery in 1943. Three generations later you can pick up the phone and talk to Bill Fleming the owner of the company.
- All levels of machinery make concrete products that can exceed ASTM standards in high quality required in the USA.
- We are totally confidential in all conversations about your company and respect your companies trade secrets and ideas.
- Heavy built machinery that uses less wear parts than most competitive machines built from other parts of the world.
- Professional Installation men are available to install, assist and train your staff at your location anywhere in the world. If anyone tells you their wet cast concrete wet cast slab and veneer stone machinery is so simple you don’t need startup training and all you need is their training video, they are either nuts or lying to you. All machinery takes training and requires instructions on how to install, operate and maintain the machinery no matter how big or small of system. The difference working with us is we will tell you the truth and make sure you know the challenges in advance so you will not have any unforeseen surprises. In doing this, you will be saving a lot of money and have machinery you can operate for decades.
- We help you design a fully operational plant and with suggestions in how to layout the equipment to work the best fit your land space or building.
- Free consulting program is free for one year after you purchase your engineered concrete wet cast slab and veneer stone machinery talking directly with Bill Fleming the president of the company. The goal is to help you with advice in any way to help grow your business.
- Personalized mix design, analysis, testing and formulations are available using your sand and rock aggregates before your machinery arrives. Your first concrete products made will be saleable and up to USA high quality standards, saving you time, money and reputation in your market.
- We will help you understand the type and qualities of production people that are needed to operate and maintain this type of plant. This can save you time and a huge amount of money by getting the correct talent of people. The cost of making bad products, having poor production efficiency and expensive production headaches can be prevented by using us in this step.
- Our people are here to help and guide you through the journey of setting up a concrete wet cast slab and veneer stone plant operation. This is important when you need to talk to us for any service questions, parts and future equipment questions.
- Optional pre-training in the North America factories and visits to plants with operating equipment are available before your machine is shipped on some model of machinery. The wet cast industry, unlike others concrete markets I deal within is a very confidential market which we must respect. I do have some customers who are willing to help you depending on your location and equipment package you have purchased.
This will include learning how to make concrete wet cast slab and veneer stone concrete products, daily operational plant procedures, operational maintenance procedures and much more. On the same trip you can have the benefit of being trained on the actual machine system your company has purchased. You will be able to inspect the machinery prior to shipment and meet the full staff of people that will be working with you in the future.
The goal is to send you back home to your site and already be 80% pre-trained before your machinery arrives at your site. This will save you start up time and make you more money than you can believe before starting production. Doing this in advance will help increase the opportunities for your business success before the service technician arrives.
- I also have available to you several sources of concrete wet cast slab and veneer stone productions molds. For an additional fee, I have available a one-day class that will teach you all the techniques that are required in learning how to manufacture the correct concrete and color wet cast slabs, cast stone and veneer stone products. You will also receive a certification certificate in veneer stone production, quality control and technical processes after completing the class.
- You will know in advance of signing any purchase agreement the total cost of the concrete wet cast slab and veneer stone machines. Included in the offer you will see the service, installation and shipment cost landed to the city or shipping port of your choice.
- Depending on your area weather conditions, availability to local parts suppliers and distance from any access to major cities or airports in the world we will put together a customized and recommended spare parts list for one year’s running operation of the machinery.
- All engineering drawings, plant layouts including electrical specifications are supplied at no charge. Electrical motors will be supplied to your countries Hertz, voltage requirements.
- The electrical motors, controls, PLC software are provided with the best quality and latest technology products available on the market. You will be provided with all the details on units so your local suppliers can supply. In addition, if your staff is already familiar with a particular brand of controls they will be able to understand how to operate the concrete wet cast slab and veneer stone machinery with better education and resources. This will save you more money and time. If you need help with obtaining parts be you become more self-reliant as a company.
For additional help in answering common questions you can click on the following link and request a copy of my booklet “The Only Buying Block Machine Guide You’ll Ever Need” The same principles to buying a concrete wet cast slab and veneer stone wet cast machines are basically the same and should greatly help you to read.
You are always welcome to email me with your questions at billfleming@globalmachinemarket.com or call my office phone at 314-960-0540.