Slab & Veneer Stone Producers:
Which Equipment is the Right Machine for You?
Get the answers you need and choose the correct slab machine system!
Are you looking to purchase a new or used concrete slab or veneer equipment system?
You’re the owner of a concrete business and ready to expand your business or replace an outdated machine to maintain existing capacity. You’ve taken a look at the options for slabs and architectural Veneer Stones machines there are limited options, but which one is the right one for you?
We work with existing and startup veneer stone and concrete slab producing companies who are challenged with finding alternatives in equipment technology to allow themselves to increase their production and reduce labor. We help them get a total one stop solution source by supplying a complete operating plant by combining all new equipment or a combination of new, reconditioned or used equipment. The end result is a complete operating plant installed up and running with factory warranty that is affordable.
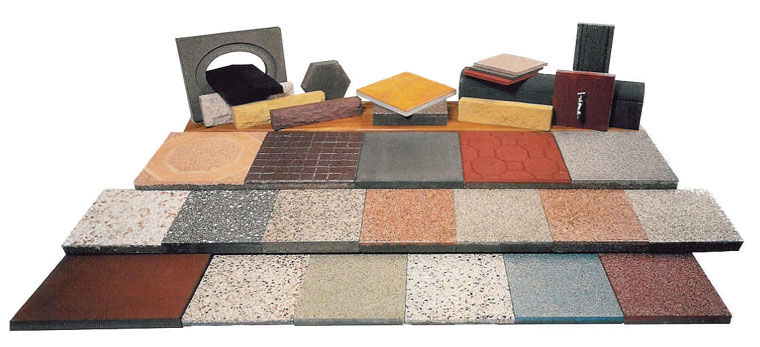
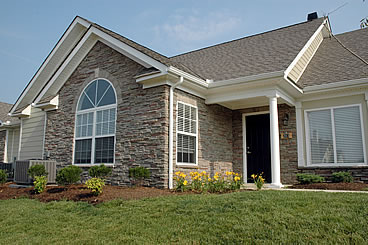
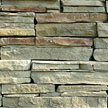
Ready to finally find which type of slab or veneer stone equipment will help you grow your company?
Choosing a wet cast slab and architectural veneer machine system is like choosing a car to purchase.
Like the car industry there are many type and sizes of Concrete Wet Cast machines systems you will have to choose from. You will find some machines make specific products at high production levels, while smaller systems might be more suited for making a wide variety of products such as Pavers, Concrete slabs, Architectural veneers, Landscape, Retaining Wall Units in a single day.
Just like buying a car if you just ask the price and catalog of a car it will leave you even more confused unless you know what you what to make, along with how many units per day and at what level of investment. If you need more help understanding which products are best suited to make on our machinery systems just e-mail me with the type of products you think you want to make and pick up the phone and call me at 314-960-0540 so I can help you.
Most all cars can go down the road at 55 mph (88 kph) however maybe you need a car that can go 100mph (160kph) or 150mph (241kph) all day long. Maybe you don’t need four seats and a large motor when a good used or pre-owned car would get you going down the road for the level of budget investment and needs for you? The same is true in choosing concrete wet cast machinery systems. In a level 1 wet cast machine system it’s like operating the fastest race car at the race track.
My goal is to help you define which level of equipment you are needing to purchase from me so you can grow your business.
I refer to the wet cast concrete products industry as having 3 Levels of Investment and production. In this section will are only going to be talking about level 2, which is the medium production level semi-automatic machinery that requires some labor in the operation.
When watching and operating this level of output production it is amazing with certain products the system can produce almost as much as a Level 1 operation. The difference in the level is the versatility and fast change over from different products that can be run in the system compared to a level 1 system which is best at mass production of a few certain products. If you are utilizing this equipment everyday with and have a labor rate that is an overpriced you may find this machine line to be a perfect fit for your operation.
Level 2 (Medium Producer) is the serious level of concrete products production. Companies are driving to produce a modest to high production output of slabs or concrete products. They need a versatile machine that can make a lot of different products at a good production rate and some products will require large production runs. Making a quality product it vital and often times specialty molds will being used so semi-automatic demolding methods will have to be used but are worth the extra cost because of the high profit margins on the products.
Plant designs normally and split between fitting into existing plant setups and planning for all new building being designed around the manufacturing equipment for operational; efficiencies. Often time’s companies or individuals are new to industry and entering the market for the first time with ideas and products is why they are exploring the machinery. The majority of users have been in business for many years either manufacturing or buying and reselling products before purchasing this level of equipment package. If they have not previously been in the industry it is important to the success of the company to have a strong sales and marketing team to sell the amount of products that this machine line can produce.
All aspects of the concrete batching, mixing, casting and palletizing processes are generally semi-automatic. Click on the link https://www.screencast.com/t/Vpuoa1bo to see a fully operational Level 2 operation.
A typical production plant would include a batch plant, concrete mixer, cement silo with all the materials being weighed and premeasured prior to being placed into the wet cast machinery. Below are the production outputs a typical plant could expect depending on your specific requirements.
Product | Production Up to in 8 Hours |
18″x18″x2″(45x45x4cm) | 6,000 units per day |
Veneer Stone | 5000/sq.ft. (465 m2 ) |
For additional help in answering common questions you can click on the following link and request a copy of my booklet “The Only Buying Block Machine Guide you will ever need” The same principles to buying a wet cast machinery are basically the same and should greatly help you to read.
You are always welcome to email me with your questions at billfleming@globalmachinemarket.com or call my office phone at 314-960-0540.
Many of the Level 2 systems are built specifically to the user’s unique product and production needs. A typical multi station wet casting production slab production machine system consist of molds that are carried and produced on Timber carriers of size 56 1/4″ x 31 1/2″ (1430mm x 800mm). The production line is designed to operate on a cycle time of approximately 16-24 seconds. The cycle time is defendant on semi-automatic functions undertaken during the manufacturing process.
TYPICIAL PRODUCTION LINE
The concrete products (variable sized) are manufactured in polyurethane molds within the carrier production area of 56 1/4″ x 31 1/2″ (1200 x 800mm) and of your choice and mounted into a suitable carriers.
The machine system consist of several individual machine components that when connected together make a complete operating system manufacturing concrete slabs and other concrete related products.
The first step in the journey of making concrete products with this machinery line is bring products back from the curing room that were produced yesterday. We will then place them into the wet cast machine system for demolding and redosing. Listed below is a general summary of the individual equipment items and descriptions that make up a wet cast system for the product of slabs, pavers and hundreds or other types of concrete products.
Single Stack Infeed Conveyor
This units holds one cured stack of carriers of yesterdays produced products. The Single Stack Infeed Conveyor automatically conveys a complete stacker of carriers into the lowerator. The infeed buffer is loaded by the same fork lift that is being used taking the freshly made products and carriers to the curing room from the elevator.
Lowerator. This device first start the process by accepting a complete stack of carriers into the unloading position. Then the Lowerator separates the carriers from each other so they individually sorted coming down the Carrier Conveyor Line.
Carrier Conveyor line
A pusher conveyor system that transports and positions the carriers to the correct stations along the wet cast system.
Carrier Turnover Station
The carrier turnover device rotates the carrier and product mold together 180 degrees and leaves the molds and concrete product separated from the carrier upside down on a belted conveyor.
The carrier is rotated back into its original position in the production line. At the same time this is occurring the product mold is being manually peeled from the product. The mold is then manually paced back on the carrier while the system is functioning but prior to dosing of concrete molds with concrete.
Spare Stations.
Spare stations are provided for the returning of the mold to the empty carrier and for the manual application of release oil if needed.
Semi – Manual Concrete Dosing System (Single Color) Station
A Single Screw Dosing system with Crisscross motion suitable for dosing the length of the carrier is normally supplied depending on requirements of product being produced.
Vibration table Stations
Once the mold has been filled with concrete the carrier is automatically moved onto the vibration stations. These combination of two stations fitted with electric vibrators and pneumatic carrier clamps vibrates and compacts the concrete so you obtain a quality high strength product. The vibration motors utilize manually adjustable weights to a preset the level of vibration amplitude force. As an option I can offer a frequency controller which will allow you to make different frequency speed adjustments to the vibrators during the cycle of making the concrete products. This is advantageous for allowing the operator to fine tune the vibration settings differently during the filling and compaction stages of making your concrete products. This will help greatly if you will be producing different product thicknesses and are looking to obtain different types of finishes on your products.
Elevator
This device is used to stack the individual carriers into a stack of carriers and then transfers mass of carriers to the Single Stack Output Conveyor. A typical stack of slabs may be stacked twenty two layers high.
Single stack Output Conveyor
This unit is designed to hold a completed stack of carriers and position the stack for a fork lift to pick up the stack. The output conveyor is unloaded by the same fork lift that is being used to load the Lowerator of the same production line. Only one fork lift is required to operate complete system.
PLC control system
The PLC (Program Logic Controller) is programmed to operate the entire system and is designed to be user friendly so several operators along the production line can stop the system at any time. The controls are based on the theory to make the machinery system smarter so the human person does not have to think as much operating the machine. This helps the producer ensure a consistent operation and make top quality products no matter what the level of knowledge the operator has in making concrete products.
Egan controls
If you have more questions about the system please feel free to give me a call at 314-960-0540
I look forward to hearing from you as soon as possible.